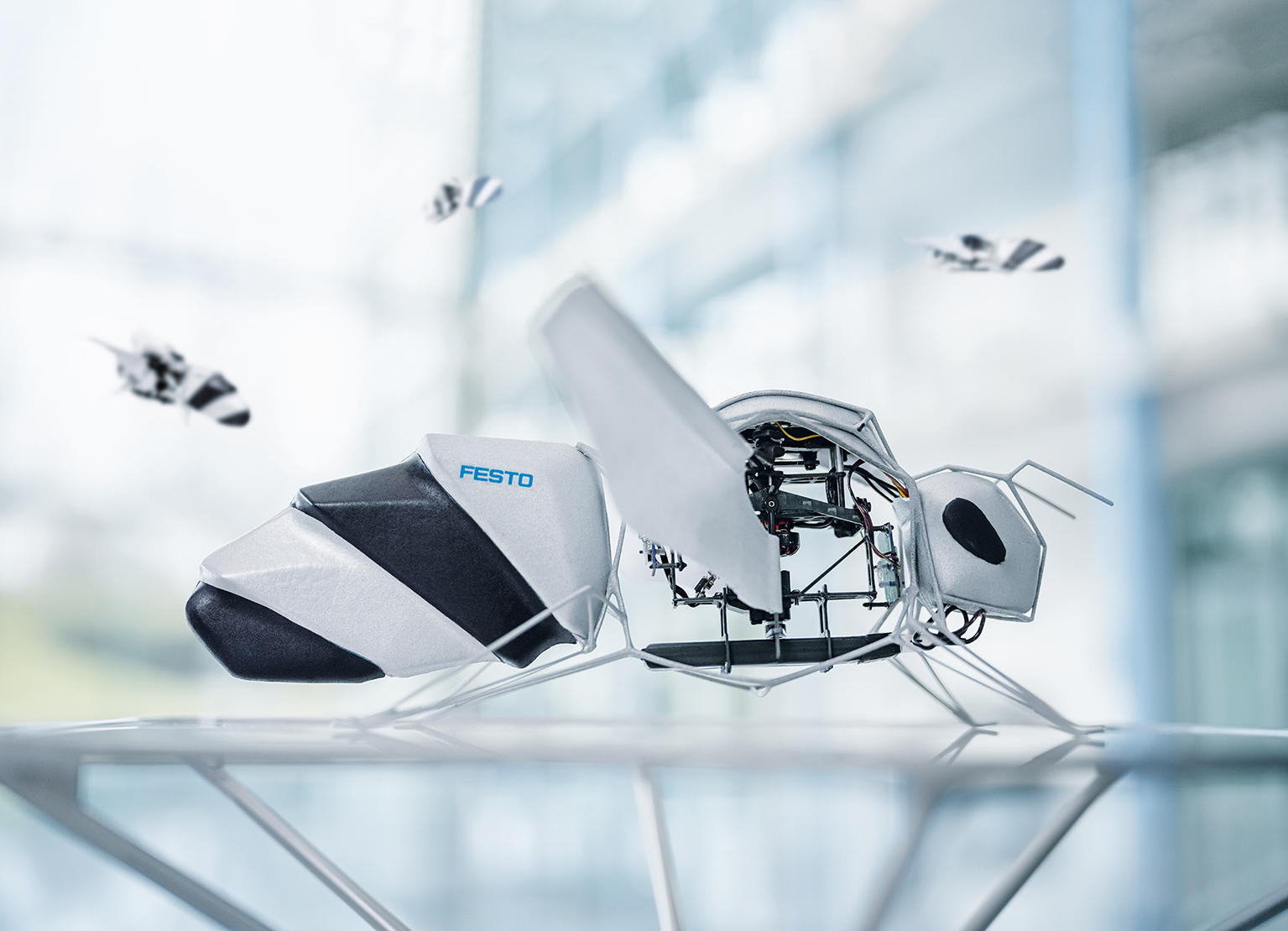
Autonomous Flying in a Swarm: BionicBee – ultralight flying object with precise control
Autonomous Flying in a Swarm
BionicBee – ultralight flying object with precise control
For more than 15 years, the Bionic Learning Network has been focusing on the fascination of flying. In addition to the technical decoding of bird flight, the team has researched and technologically implemented numerous other flying objects and their natural principles. With the BionicBee, the Bionic Learning Network has now for the first time developed a flying object that can fly in large numbers and completely autonomously in a swarm. The BionicBee will present its first flight show at the Hannover Messe 2024.
At around 34 grams, a length of 220 millimetres and a wingspan of 240 millimetres, the BionicBee is the smallest flying object created by the Bionic Learning Network to date. For the first time, the developers used the method of generative design: after entering just a few parameters, a software application uses defined design principles to find the optimal structure to use as little material as necessary while maintaining the most stable construction possible. This consistent lightweight construction is essential for good manoeuvrability and flying time.
Autonomous flying in a swarm
The autonomous behavior of the bee swarm is achieved with the help of an indoor locating system with ultra-wideband (UWB) technology. For this purpose, eight UWB anchors are installed in the space on two levels. This enables an accurate time measurement and allows the bees to locate themselves in the space. The UWB anchors send signals to the individual bees, which can independently measure the distances to the respective transmitting elements and calculate their own position in the space using the time stamps.
To fl y in a swarm, the bees follow the paths specified by a central computer. To ensure safe and collision-free flight in close formation, a high degree of spatial and temporal accuracy is required. When planning the path, the possible mutual interaction through air turbulence “downwash” must also be taken into account.
As every bee is handmade and even the smallest manufacturing differences can influence its flight behavior, the bees additionally have an automatic calibration function: After a short test fl ight, each bee determines its individually optimized controller parameters. The intelligent algorithm can thus calculate the hardware differences between the individual bees, allowing the entire swarm to be controlled from outside, as if all bees were identical.
BionicBee 1. The BionicBee is the smallest flying object of the Bionic Learning Network to date. For the first time, the developers used the methodology of generative design.